弊社のフィルター/技術へのチャレンジは、社会/環境的な背景が大きく関係します。
背景とそれに伴う技術向上への挑戦への軌跡をご紹介します。
過去のトンネル換気は送風機で外気を送り込むだけ、もしくは排気させるのみしか方法がなく、坑内の清浄度は高くありませんでした。
そのため、劣悪な環境で作業する方々が「トンネルじん肺」に悩まされ、トンネル建設工事における有所見者数は実に年間で1000人以上にものぼり、社会問題となっておりました。
作業環境の改善が急務と考えられ、解決のためにと、工事用集塵機の開発に乗り出しました。
開発の障壁
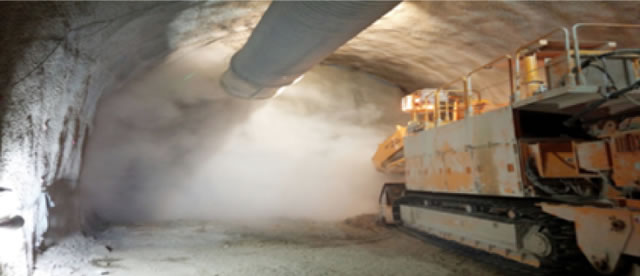
しかも有害な結晶質シリカ成分も多く、トンネルでじん肺の原因となっていました。
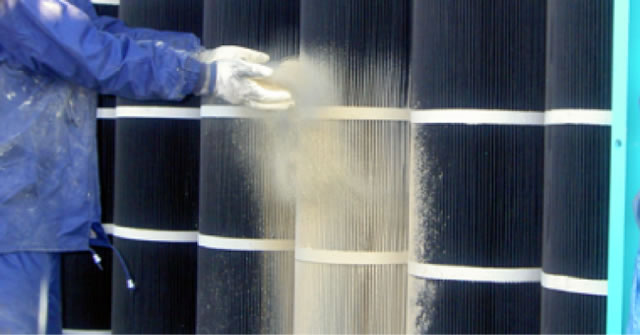
また、高湿度かつ24時間連続作業は過酷な環境でフィルターを目詰まりさせる要因が多く、連続的な集塵は困難でした。
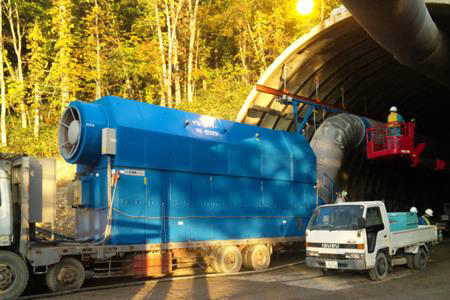
成果 Achievment
大型集塵換気方式の採用が広まり、劣悪であった作業環境が飛躍的に改善され、
今ではトンネルじん肺患者は1/100に激減しています。
トンネル業界シェア75%(年間150台)
トンネル工事で解決した難課題を工業用集塵機の開発へつなげ主力商品化。
工業用集塵機Iシリーズは、トンネル工事用集塵機で培ったフィルター応用技術で、標準仕様で大気塵レベルの高い清浄度、装置の省スペース化、フィルターのメンテナンスフリーを実現しました。 今までの一般産業用集塵機では克服が困難であった”難題”を打ち破る画期的な製品です。
開発の障壁
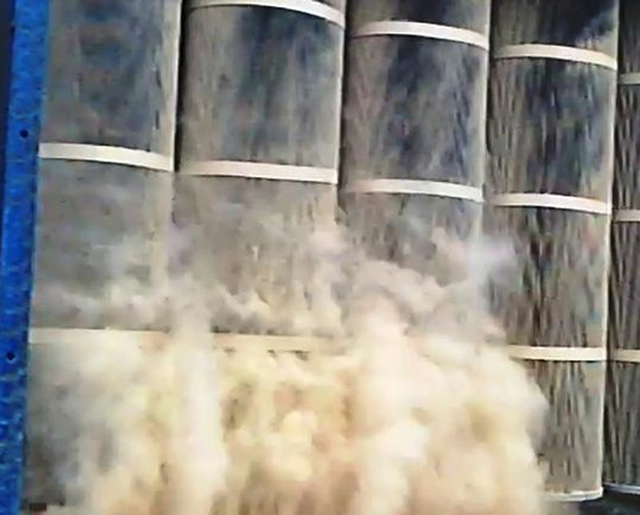
工業用集塵機で採用されていたプリーツフィルターは目詰まりしやすい=管理手間がかかる、工場のラインが止まる、という印象により苦手意識を持たれやすい特性がありました。
克服→独自のフィルター再生機構と表面ろ過によって、フィルター深層での目詰まりが発生しません。
独自のフィルター再生機構はこちらをご覧ください
フィルター表面の付着粉塵が強力なエアパルスを発生することによって、綺麗に剥離できています。
1:弊社集塵機はフィルター1本に対し1つのエアパルス弁を有しているため、フィルターに対するパルスの伝達ロスが少ないです。
2:エアパルス弁から開放された圧縮空気が瞬間的に亜音速域に達することで、衝撃波に近い物理的要素によりクリーニングできています。
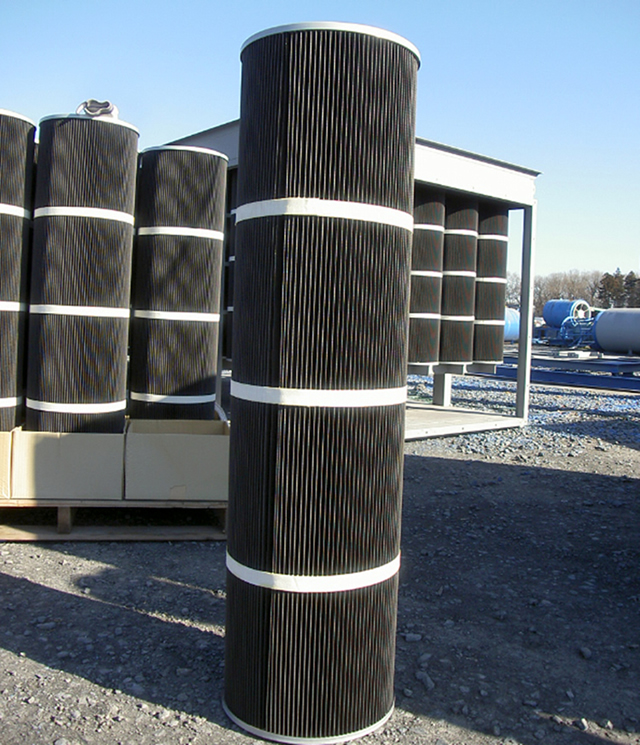
工業用集塵機で広く採用されている一般的なバグフィルターは「使い捨て」「フィルター脱落」「交換本数が多い」ことによるメンテナンスやフィルター交換の手間と費用がかかるといった悩みが多くありました。
1:硬質エレメント成型フィルターを採用しており、洗浄を容易にします。(ローテーション利用を可能に)
2:フィルター上下端部が金属皿であることで強固に固定されます。これまで運用実績で脱落は皆無です。
3:フィルター1本あたりのろ過面積が大面積なので、交換本数も少なく、工期が短縮できます。
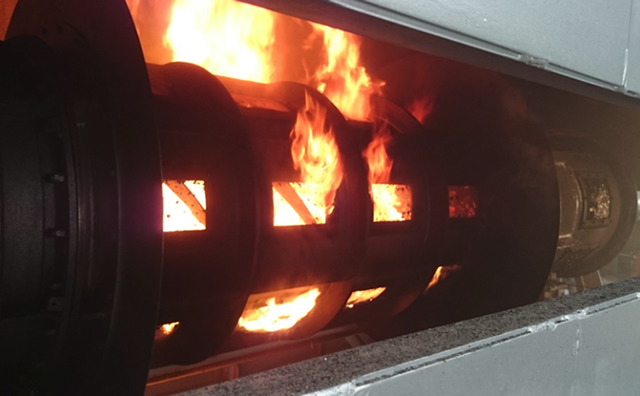
2013年より、大気汚染の指標がPM10→PM2.5へ移行し、排気清浄度を上げなければならなくなった工場が増加しました。工場建屋で発生する粉じんは、トンネル工事以上に微細である、研磨性が高い、高温ガスを含んでいる、等トンネル工事とは異なるニーズがありました。
5μm99.00%~0.15μm99.95%のろ過精度を有し、一般的なバグフィルターに比べろ過性能が優れています。
金属ヒュームや溶射粉じんをはじめとしたPM2.5、バグインバグアウト、高温排気ガスなど、お客様ごとの特殊な課題もクリアにしてきました。
成果 Achievment
高温ガス冷却、可動フード、3Dダクトの開発でさらに進化!
大気処理で培ったフィルター技術を、現場のお客様からたびたび悩みを耳にする、水の再生処理に生かせないものか…
要素研究を進めている最中、東日本大震災由来の福島第一原発事故が発生しました。
汚染水処理試験装置の採用をきっかけに、水処理という新たな困難に当たり、本格的な装置開発を始めました。
開発の障壁
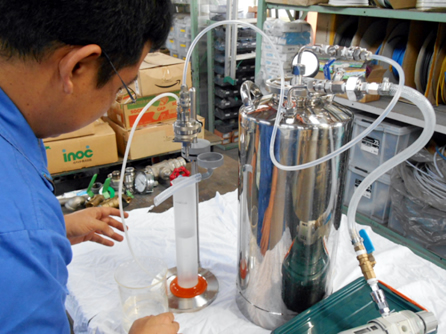
ろ過における既存技術には中空糸膜、平膜とあります。既存技術との差別化を図るために、弊社製品の特徴でもあるプリーツフィルターでどんな価値が生み出せるか試験を重ねました。
その結果、粘土質高濃度濁度の清澄化に成功しました。
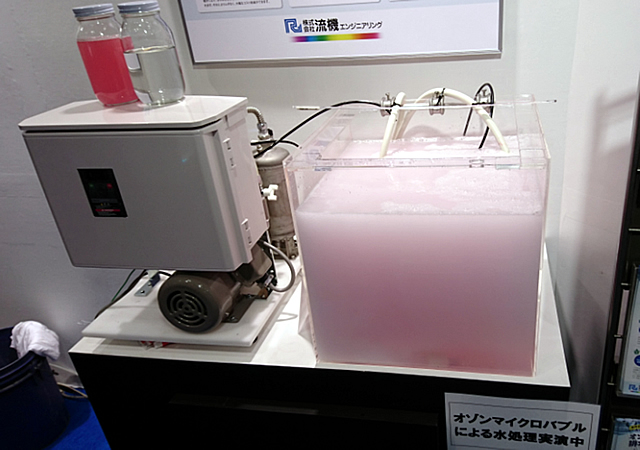
お客様のお悩みの中で、特に困難とされたことが「脱色」、「臭気」、「油分」など難分解性有機物質でした。
これらを解決に導いたものがオゾン+マイクロバブルによる分解です。
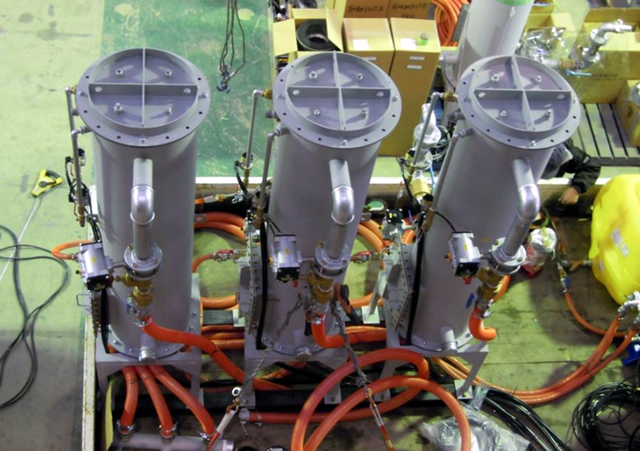
難分解性有機物質と同じくして、ろ過前後処理技術のニーズも多く、脱水乾燥、凝集、濃縮、中和…とさまざまなお悩みの声を耳にします。
水処理技術の可能性を広げるために、お客様と一丸となって実地テスト、検証を繰り返しています。弊社では「既存装置の提供」ではなく、習得した技術を駆使した「水ソリューション」を提案していくようになりました。
成果 Achievment
濃縮装置、平膜脱水乾燥装置の開発でさらに進化…
廃棄物資源化、ダイオキシン類処理、アスベスト処理、VOC回収、汚染土壌浄化、除湿 、脱臭、CO2吸着回収…etc
環境における課題が存在し続ける限り、流機エンジニアリングの技術は成長し続けていきます。